Root Cause Analysis – RCA: Hướng dẫn đầy đủ cho các nhà sản xuất
Trong sản xuất, có những thời điểm các hoạt động sản xuất có thể trở nên hỗn loạn, nhanh chóng và phức tạp, khiến nhà sản xuất phải đối mặt với những vấn đề đặc biệt và rất nan giải. Những vấn đề này có thể làm giảm tốc độ sản xuất, gây ra tắc nghẽn hoặc thậm chí phải dừng sản xuất một cách bất ngờ. Để giải quyết những vấn đề này, nhiều người đã áp dụng phân tích nguyên nhân gốc (Root Cause Analysis – RCA) để tìm hiểu và thực hiện các giải pháp. Trong bài viết này, hãy cùng Comit Corporation đi tìm hiểu về Root Cause Analysis là gì? Tại sao nên dùng phương pháp Root Cause Analysis nhé!
Root Cause Analysis (RCA) là gì?
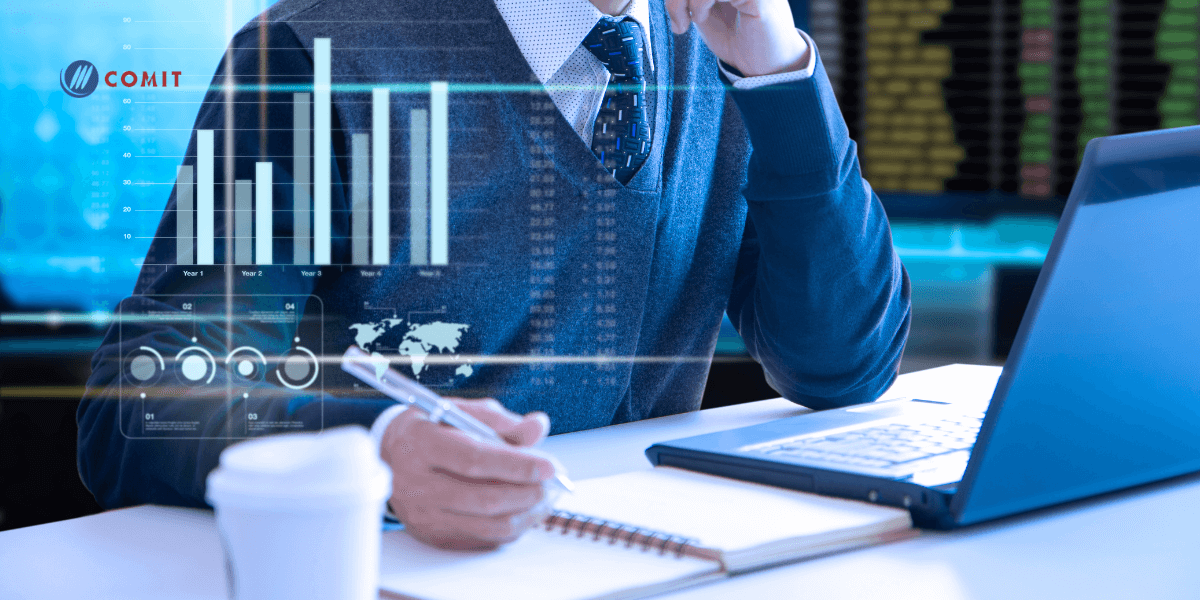
Phân tích nguyên nhân gốc (RCA) là gì? Phân tích nguyên nhân gốc (RCA) là một quy trình cụ thể nhận ra rằng sự gián đoạn và vấn đề có thể được truy vết về một nguyên nhân cụ thể và rằng giải pháp để sửa chữa nguyên nhân đó sẽ lan tỏa và dẫn đến một trạng thái cải thiện. RCA cố gắng xác định nguyên nhân của khuyết điểm và vấn đề thay vì chỉ điều trị triệu chứng hoặc “dập lửa”.
Phân tích nguyên nhân gốc được coi là một yếu tố quan trọng trong cả phương pháp sản xuất hòa nhập và Six Sigma. Nó tối ưu hóa thời gian cần thiết để phân tích sâu vào nguyên nhân của một vấn đề và cung cấp một cấu trúc để giải quyết vấn đề trong quá trình sản xuất.
Lợi ích của phân tích nguyên nhân gốc
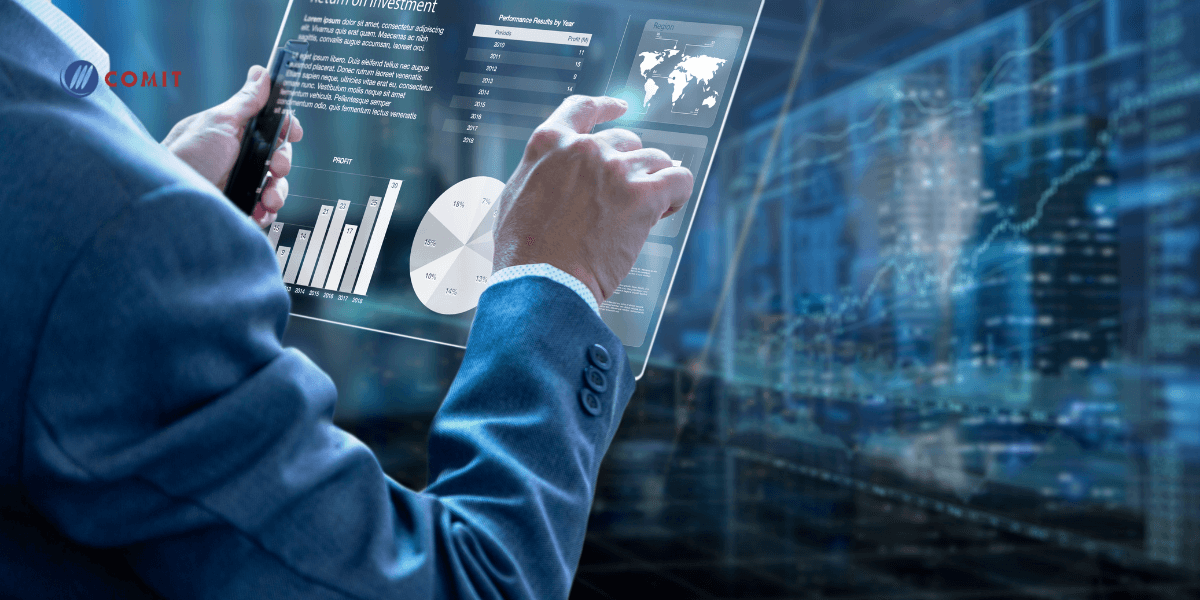
Phân tích nguyên nhân gốc (Root Cause Analysis – RCA) mang lại nhiều lợi ích quan trọng cho các tổ chức và doanh nghiệp trong nhiều lĩnh vực khác nhau, đặc biệt hơn cả là lĩnh vực sản xuất. Dưới đây là một số lợi ích của phân tích nguyên nhân gốc mà Comit Corporation đã tổng hợp bao gồm:
Tiết kiệm chi phí
Do phân tích nguyên nhân gốc tập trung vào “bệnh” chứ không chỉ là “triệu chứng” hay có thể gọi là tập trung vào nguyên nhân cốt lõi nên nó giúp giảm thiểu chi phí bằng cách giảm thời gian chết máy, giảm số lượng khuyết điểm và cải thiện quy trình. Bằng cách tìm ra nguyên nhân gốc của vấn đề, RCA giúp tránh lãng phí thời gian và chi phí trong việc giải quyết những vấn đề lặp đi lặp lại. Thay vì chỉ điều trị triệu chứng mỗi lần vấn đề xuất hiện, việc giải quyết nguyên nhân gốc giúp ngăn chặn các vấn đề tương tự xảy ra trong tương lai.
OEM là gì? OEM là viết tắt của “Original Equipment Manufacturer,” tiếng Việt có thể hiểu là “Nhà sản xuất thiết bị gốc” hoặc “Nhà sản xuất trang thiết bị ban đầu.” OEM là một công ty hoặc tổ chức sản xuất các thành phần hoặc sản phẩm cuối cùng mà sau đó sẽ được sử dụng hoặc bán dưới tên thương hiệu của một công ty khác.
Tối ưu hoá
Nhiều công ty sản xuất hoạt động với các quy trình một phần bị hỏng. Phân tích nguyên nhân gốc giúp tối ưu hóa quy trình để cung cấp các giải pháp thực tế và thiết lập các quy trình chuẩn theo đúng quy trình.
Tự động hóa
Hiện nay, nhà máy có truy cập và cái nhìn sâu hơn về dữ liệu hơn bao giờ hết. Dữ liệu này có thể được phân tích và bám vào bối cảnh để làm cho phân tích nguyên nhân gốc trở nên dễ tiếp thu cho các bộ phận và nhà máy khác trong cùng một công ty. Điều này giúp cải thiện hiệu quả và giảm thời gian chết máy.
Chính xác
Vì việc tự động hóa thông qua phân tích dữ liệu lý tưởng cho kết quả phân tích nguyên nhân gốc, các vấn đề về an toàn, bảo dưỡng và chất lượng có thể được dự đoán chính xác hơn và có thể được giải quyết nhanh chóng để giảm thiểu thời gian chết máy.
Cách thực hiện phân tích nguyên nhân gốc
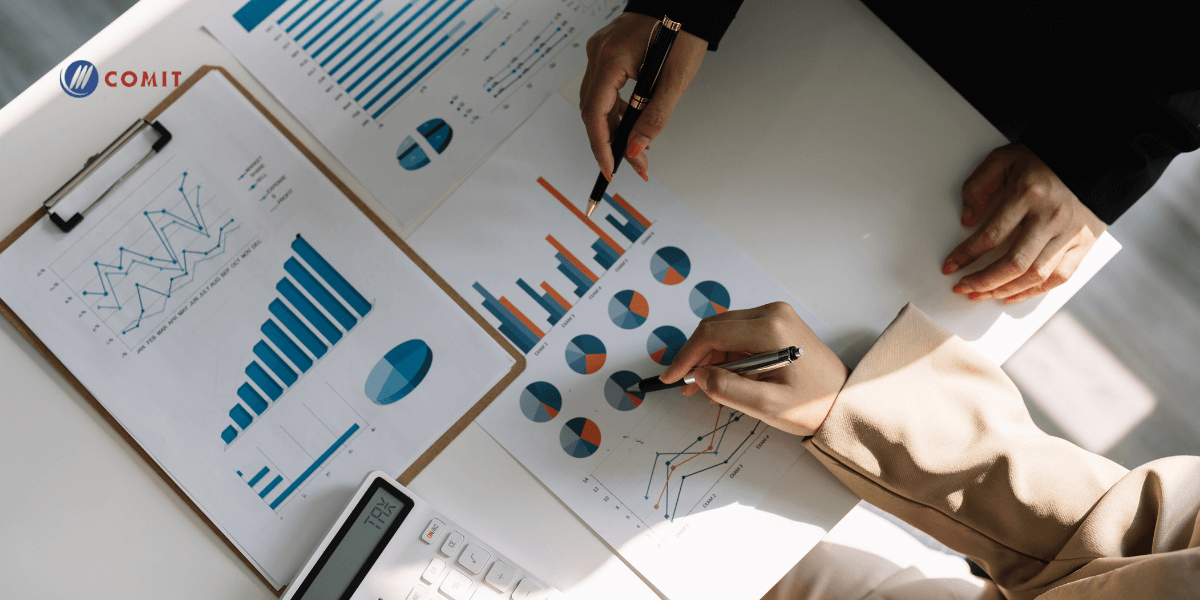
Phương pháp tiến hành phân tích nguyên nhân gốc có thể khác nhau từ công ty này đến công ty khác cũng như từ vấn đề này sang vấn đề khác. Nó có thể tập trung vào vấn đề cụ thể của máy chủ đối với một loại máy cụ thể của OEM nhất định. Nó cũng có thể được sử dụng để phân tích chướng ngại giữa các phòng ban. Hoặc nó có thể được sử dụng để giải quyết khuyết điểm trên toàn nhà máy trong một doanh nghiệp. Nhìn chung, có sáu bước thường xuyên tham gia vào phân tích nguyên nhân gốc:
Xác định vấn đề
Bước đầu tiên là quan trọng nhất. Tất cả các thành viên trong nhóm phải hiểu rõ vấn đề. Nó phải được nêu một cách khách quan. Và nó đòi hỏi câu hỏi làm rõ để xác định rằng đó là một vấn đề khẩn cấp hoặc chướng ngại. Đây là giai đoạn rộng nhất và là tuyên bố vấn đề tổng quát như tỷ lệ khuyết điểm, chướng ngại hoặc gửi hàng bị bỏ sót.
Thu thập dữ liệu
Thu thập dữ liệu là rất quan trọng trong phân tích nguyên nhân gốc. Ở đây, các thành viên của nhóm cố gắng liệt kê càng nhiều yếu tố gây ra càng tốt. Mọi thứ đều được cân nhắc, và danh sách có thể là rộng và chi tiết. Ngày nay, việc tìm và tận dụng dữ liệu trong phân tích nguyên nhân gốc dễ dàng hơn bao giờ hết, vì nhiều nhà sản xuất thiết bị OEM đã tích hợp thu thập dữ liệu vào các máy móc của họ. Có thể xảy ra trường hợp nhà máy đã triển khai các thiết bị thu thập dữ liệu cho những máy không chứa nó theo cách tự nhiên.
Phân tách nguyên nhân khỏi triệu chứng
Thường thì việc nhầm lẫn giữa triệu chứng và nguyên nhân là phổ biến. Một số công cụ và phương pháp có thể giúp phân chia nguyên nhân khỏi triệu chứng. Giả định là nếu có thể xác định và sửa chữa được nguyên nhân, triệu chứng sẽ ngừng tồn tại. Ở đây, việc thu thập dữ liệu cũng có thể là rất quan trọng, vì nhiều hệ thống thu thập dữ liệu có khả năng phân tích để xác định các danh mục vấn đề.
Xác định biện pháp sửa chữa
Khi nguyên nhân gốc đã được xác định, có thể tạo ra một giải pháp hiệu quả. Điều này có thể bao gồm đào tạo, sửa đổi cơ khí, bố trí sàn, hoặc năng lực phân tích dữ liệu và thu thập dữ liệu mạnh mẽ hơn. Thường thì dữ liệu có thể hỗ trợ trong việc tạo ra biện pháp sửa chữa. Bằng cách có dữ liệu và hiểu biết thời gian thực trong tay khi xác định nguyên nhân gốc, các quản lý có thể tạo ra một giải pháp thực tế, dựa trên dữ liệu thực tế.
Triển khai giải pháp
Sau khi xác định nguyên nhân gốc và nhận dạng biện pháp sửa chữa, nhóm phải triển khai giải pháp. Điều này có nghĩa là sửa đổi hoặc thay thế các quy trình cũ, tạo ra luồng công việc mới và kiểm tra kết quả. Mức độ của khả năng thu thập dữ liệu càng sâu, tác động của phân tích sẽ càng lớn đối với giải pháp được chọn. Có thể thậm chí có khả năng lập trình hành động tự động hoặc bán tự động bởi các máy để giúp thực hiện hoặc theo dõi tiến trình giải pháp hoặc tác động lên quá trình phát triển của nó.
Xác minh và mở rộng kết quả
Không có giải pháp nào tồn tại lâu dài mà không có quy trình kiểm tra. Phần xác minh này phải xác nhận tính hiệu quả của giải pháp. Việc thu thập dữ liệu chặt chẽ và chịu phân tích thời gian thực giúp kiểm tra hoặc điều chỉnh tính hiệu quả của giải pháp. Nếu giải pháp thành công, nguyên nhân gốc có thể chuyển đổi sang các quy trình và phòng ban khác trong công ty.
Các công cụ và phương pháp
Phân tích nguyên nhân gốc có thể được thực hiện bằng cách thủ công bởi một nhóm. Nhưng khi kết hợp với việc thu thập và phân tích dữ liệu tiên tiến, nó sẽ cả tăng tốc và cải thiện tác động. Các giải pháp có thể được triển khai cho các nhà máy và các phòng ban khác gặp phải các vấn đề tương tự, và nó cũng có thể cải thiện hiệu suất sản xuất và giảm thiểu khuyết điểm trong sản xuất.
Có nhiều công cụ và phương pháp khác nhau để thực hiện phân tích nguyên nhân gốc (Root Cause Analysis – RCA). Sử dụng các công nghệ tự động hóa trong việc thu thập và phân tích dữ liệu thời gian thực từ các máy móc và quy trình sản xuất có thể giúp cải thiện hiệu quả của phân tích nguyên nhân gốc. Công nghệ này cung cấp dữ liệu chính xác và phân tích nhanh chóng, giúp xác định và giải quyết các nguyên nhân gốc một cách hiệu quả hơn. Và dưới đây là một số phương pháp phổ biến:
The Five Whys
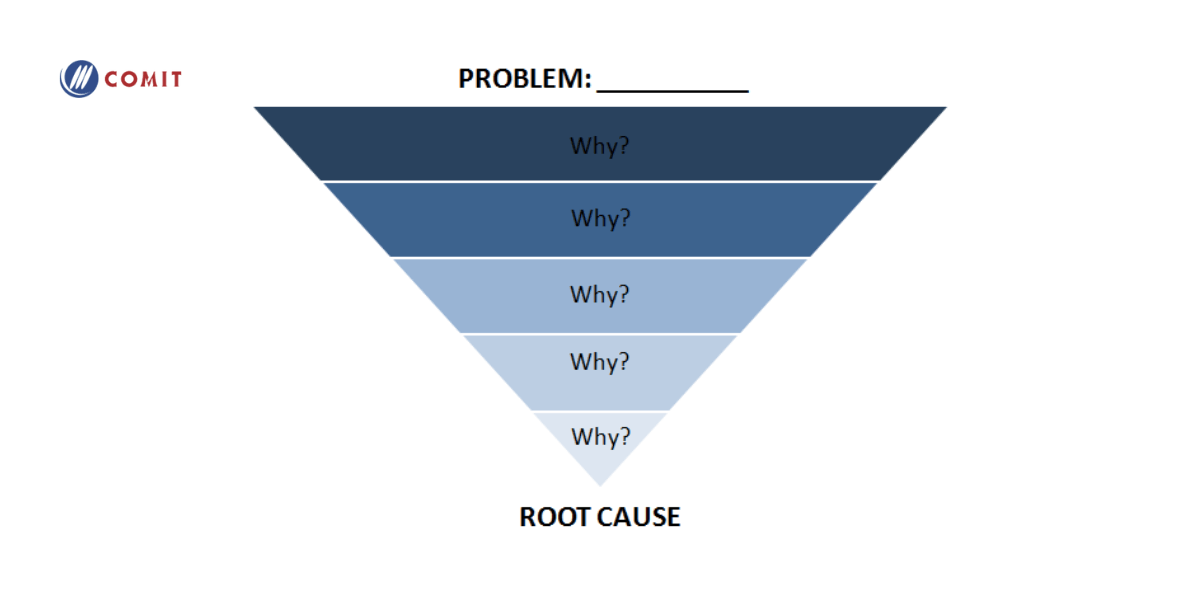
Phương pháp “Năm Lý Do Tại Sao” (The Five Whys) là một công cụ sáng tạo và mạnh mẽ được đưa ra bởi Sakichi Toyoda, người sáng lập Tập đoàn Toyota, và sau đó được phát triển và áp dụng rộng rãi trong hệ thống quản lý chất lượng Lean và Six Sigma. Mục tiêu chính của phương pháp này là tìm hiểu nguyên nhân gốc của một vấn đề, chứ không chỉ dừng lại ở cấp độ hiện tượng hay triệt tiêu các triệu chứng.
Cách thức hoạt động của phương pháp này rất đơn giản. Khi gặp một vấn đề, người thực hiện RCA hỏi liên tiếp câu hỏi “Tại sao?” năm lần, tìm kiếm các câu trả lời về nguyên nhân đằng sau từng câu hỏi. Câu trả lời của câu hỏi thứ hai sẽ trở thành câu hỏi thứ ba, và tiếp tục cho đến khi không còn câu trả lời nào khả thi. Thông qua việc hỏi liên tiếp như vậy, người thực hiện RCA tiếp cận vấn đề một cách chi tiết và sâu sắc, đạt đến nguyên nhân cốt lõi của vấn đề.
Fishbone Diagram
Biểu đồ xương cá là gì? Biểu đồ xương cá (Fishbone Diagram) là một công cụ phân tích mạnh mẽ được phát triển bởi nhà kinh tế học người Nhật Ishikawa Kaoru vào những năm 1940. Ông đã đưa ra ý tưởng này để giúp nhà sản xuất và doanh nghiệp hiểu rõ hơn về nguyên nhân gốc của các vấn đề phức tạp trong quy trình sản xuất và quản lý. Từ đó, biểu đồ xương cá đã trở thành một công cụ phổ biến trong phân tích nguyên nhân gốc và quy trình cải tiến.
Biểu đồ xương cá được gọi là “xương cá” vì khi được vẽ, nó có hình dạng giống như xương của một con cá. Trong biểu đồ, vấn đề cụ thể sẽ được đặt ở phía bên phải của biểu đồ, ở giữa, như một “đầu” của con cá. Từ vấn đề này, các đường “xương” được kéo ra, đại diện cho các nguyên nhân có thể góp phần vào vấn đề. Những nguyên nhân này được phân loại vào các danh mục chính, như “Nhân lực”, “Vật liệu”, “Phương pháp”, “Môi trường”, “Dữ liệu” và “Thiết bị”. Các danh mục này tạo thành các “xương” chính của biểu đồ và giúp tổ chức các yếu tố liên quan đến vấn đề theo từng loại.
Failure Mode and Effects Analysis – FMEA
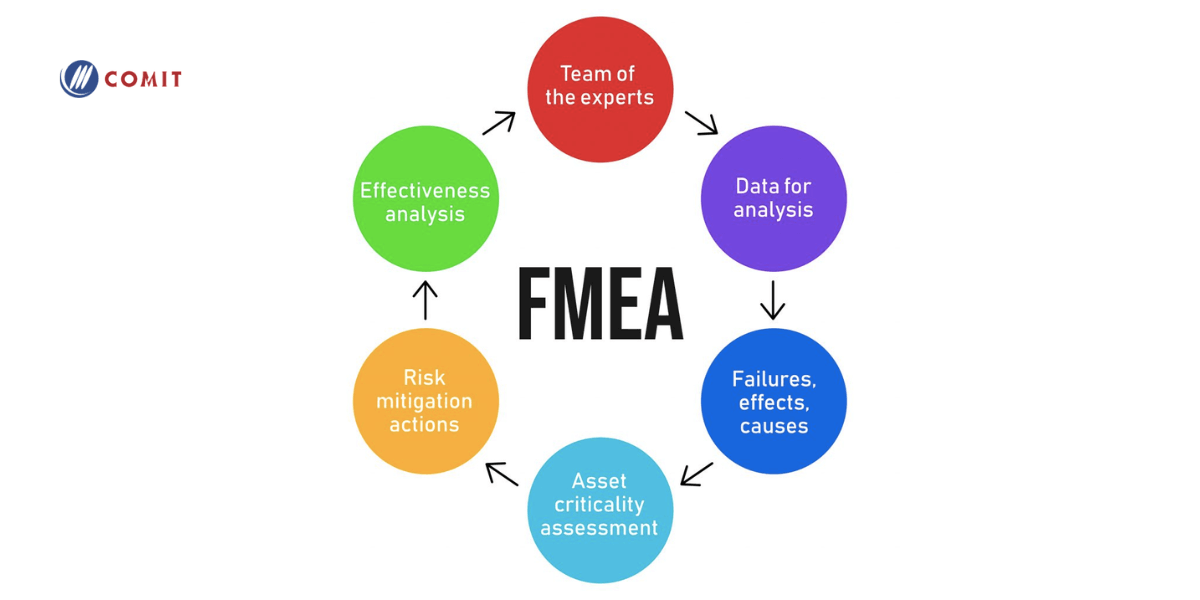
Phương pháp Failure Mode and Effects Analysis (FMEA) là một công cụ quan trọng trong phân tích nguyên nhân gốc và quản lý chất lượng. Nó thường được áp dụng trong các lĩnh vực sản xuất sản phẩm phức tạp như ô tô, hàng không và vũ trụ, y tế và công nghệ cao. Mục tiêu chính của FMEA là tìm hiểu các cách thức mà một sản phẩm có thể thất bại hoặc gặp sự cố, từ đó giúp ngăn ngừa và giảm thiểu các nguy cơ tiềm năng.
Quá trình FMEA thường được thực hiện bởi một nhóm đa chuyên ngành, bao gồm các chuyên gia từ khâu thiết kế, kỹ thuật, sản xuất, kiểm tra chất lượng và dịch vụ khách hàng. Nhóm này cùng nhau đi qua từng bước của FMEA để xác định các vấn đề tiềm ẩn và tìm ra các biện pháp phòng ngừa.
Bước đầu tiên trong FMEA là xác định các yếu tố trong sản phẩm hoặc quy trình sản xuất có thể gây ra lỗi. Các yếu tố này được gọi là “failure modes” – tạm dịch là các chế độ hỏng hóc. Đó có thể là các lỗi vật lý, hỏng hóc trong quy trình sản xuất, hỏng hóc trong vận hành hoặc sự cố trong điều kiện sử dụng. Ví dụ, trong một chiếc ô tô, failure modes có thể bao gồm hỏng động cơ, hỏng hệ thống phanh hoặc hỏng hộp số.
Sau đó, nhóm đánh giá tác động của từng failure mode. Tức là, họ đánh giá các hậu quả của việc xảy ra failure mode đó, như an toàn bị đe dọa, chất lượng sản phẩm giảm, hoặc khả năng sản phẩm không hoạt động đúng cách.
Tiếp theo, nhóm xác định các nguyên nhân gốc của các failure modes. Điều này có thể bao gồm các yếu tố như thiết kế không chính xác, chất lượng vật liệu không đảm bảo, sai sót trong quy trình sản xuất hoặc sự cố trong máy móc. Sau khi đã xác định được các failure modes và nguyên nhân gốc, nhóm tiến hành đánh giá mức độ ưu tiên của từng vấn đề. Điều này giúp xác định các vấn đề quan trọng cần được ưu tiên giải quyết. Các vấn đề quan trọng hơn sẽ được ưu tiên cao hơn trong việc triển khai biện pháp phòng ngừa.
Cuối cùng, nhóm đề xuất các biện pháp phòng ngừa và cải tiến để ngăn ngừa các failure modes xảy ra hoặc giảm thiểu tác động của chúng. Các biện pháp này có thể bao gồm thay đổi thiết kế, cải thiện quy trình sản xuất, sử dụng vật liệu tốt hơn hoặc cải tiến hệ thống kiểm tra chất lượng.
Fault Tree Analysis – FTA
Phương pháp này thường được sử dụng trong các hệ thống an toàn quan trọng, nơi các sự cố kỹ thuật có thể gây ra hậu quả nghiêm trọng. FTA giúp hiểu cách các lỗi và sự cố có thể xảy ra, từ đó giúp thiết kế hệ thống để đối phó hoặc loại bỏ các yếu tố gây lỗi.
Pareto Chart
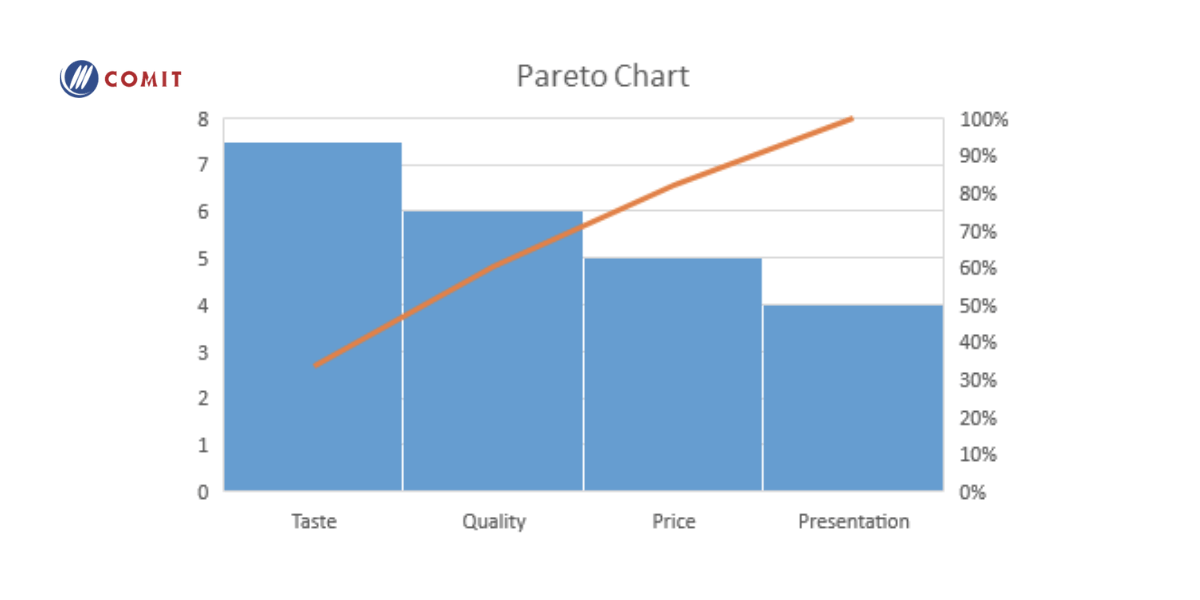
Biểu đồ Pareto là một công cụ trực quan giúp xác định các vấn đề quan trọng và ưu tiên theo mức độ quan trọng. Nó cho phép người thực hiện RCA tập trung vào những vấn đề quan trọng nhất đầu tiên để giải quyết.
Biểu đồ Pareto là gì? Biểu đồ Pareto là biểu đồ được đặt tên theo nhà kinh tế học người Ý Vilfredo Pareto, người đã phát triển khái niệm “nguyên tắc 80/20”. Nguyên tắc này cho rằng 80% các kết quả xuất hiện do 20% nguyên nhân gốc. Trong ngữ cảnh phân tích nguyên nhân gốc, nguyên tắc 80/20 áp dụng ý tưởng rằng một số nhỏ các nguyên nhân quan trọng góp phần lớn vào các vấn đề và lỗi trong quá trình sản xuất.
Biểu đồ Pareto thường được biểu diễn bằng cột dọc, sắp xếp theo thứ tự giảm dần của tần suất xuất hiện. Cột dài nhất thường đại diện cho nguyên nhân quan trọng nhất góp phần nhiều nhất vào vấn đề. Các cột khác theo sau đại diện cho các nguyên nhân khác, giảm dần theo mức độ quan trọng.
Cách sử dụng biểu đồ Pareto trong phân tích nguyên nhân gốc là bắt đầu bằng việc thu thập dữ liệu về các vấn đề và lỗi liên quan đến quy trình sản xuất. Các vấn đề này có thể bao gồm các loại lỗi, tắc nghẽn, thiếu sót trong quy trình, sự cố máy móc và hơn thế nữa. Sau đó, dữ liệu này được sắp xếp theo thứ tự giảm dần của tần suất xuất hiện.
Is/Is Not Analysis
Phương pháp Is/Is Not Analysis là một công cụ phân tích nguyên nhân gốc đơn giản và hiệu quả. Khi thực hiện phân tích này, người thực hiện sẽ tạo hai danh sách, một danh sách về những yếu tố có liên quan (Is) và một danh sách về những yếu tố không liên quan (Is Not) đến vấn đề cụ thể đang được nghiên cứu.
Việc tạo hai danh sách này giúp tập trung vào các điều kiện và yếu tố thực sự có ảnh hưởng đến vấn đề, đồng thời loại bỏ những điều không có liên quan, giúp giảm thiểu sự mơ hồ và tập trung vào những gì quan trọng nhất. Quá trình Is/Is Not Analysis đòi hỏi sự suy luận và phân loại chặt chẽ từ người thực hiện, đảm bảo rằng tất cả các điểm quan trọng được đưa vào danh sách Is, trong khi các điểm không liên quan được đưa vào danh sách Is Not.
Một ví dụ về việc áp dụng phương pháp Is/Is Not Analysis là khi một nhà sản xuất đối diện với một vấn đề về chất lượng sản phẩm. Họ sẽ bắt đầu bằng việc xác định các điều kiện hoặc yếu tố có liên quan đến vấn đề như quy trình sản xuất, nguyên liệu sử dụng, thiết bị và công nghệ sản xuất. Những yếu tố này sẽ được ghi vào danh sách Is. Tiếp theo, họ sẽ xác định các yếu tố không có liên quan như điều kiện thời tiết, vị trí địa lý của nhà máy, hay những yếu tố nằm ngoài quy trình sản xuất. Những yếu tố này sẽ được ghi vào danh sách Is Not.
Sau khi hoàn thành phân loại, nhà sản xuất sẽ tập trung vào nghiên cứu và giải quyết các yếu tố có liên quan, loại bỏ các yếu tố không liên quan, từ đó cải thiện chất lượng sản phẩm và quy trình sản xuất tổng thể. Phương pháp Is/Is Not Analysis giúp loại bỏ sự phân tán và đảm bảo rằng tập trung vào các yếu tố quan trọng nhất để giải quyết vấn đề một cách hiệu quả và tiết kiệm thời gian.
Tùy thuộc vào tình huống cụ thể, người thực hiện RCA có thể sử dụng một hoặc nhiều công cụ và phương pháp trên để xác định và giải quyết các nguyên nhân gốc của vấn đề.