Nhà Máy Thông Minh: Giải Pháp Win-Win Mang Lại Sự Tối Ưu Cho Ngành Sản Xuất
Hãy cùng COMIT tìm hiểu về Smart Factory (Nhà Máy Thông Minh): Giải Pháp Win-Win Mang Lại Sự Tối Ưu Cho Ngành Sản Xuất trong bài viết dưới đây nhé!
Nhà máy thông minh có tiềm năng tăng cường năng suất lao động ba lần trong thập kỷ tới, theo báo cáo của Deloitte. Quá trình số hóa sản xuất đang nhanh chóng tích hợp các công nghệ mới như IoT công nghiệp, phân tích dữ liệu lớn, môi trường đám mây, giao tiếp M2M (máy đến máy), trí tuệ nhân tạo và học máy.
Tiếp cận Industry 4.0 có thể đối mặt với thách thức đối với những doanh nghiệp chậm tiếp cận những thay đổi mới do tăng tốc của IIoT. Bằng cách kết hợp linh hoạt các công nghệ số tiên tiến, ngành sản xuất có khả năng hội tụ thế giới số và thế giới vật lý thông qua giá trị độc đáo của thông tin trong chuỗi cung ứng. Hãy cùng đi sâu vào từng chi tiết để hiểu rõ hơn về các công nghệ có khả năng tối ưu hóa hoạt động, quy trình và tài sản.
Smart Factory là gì?
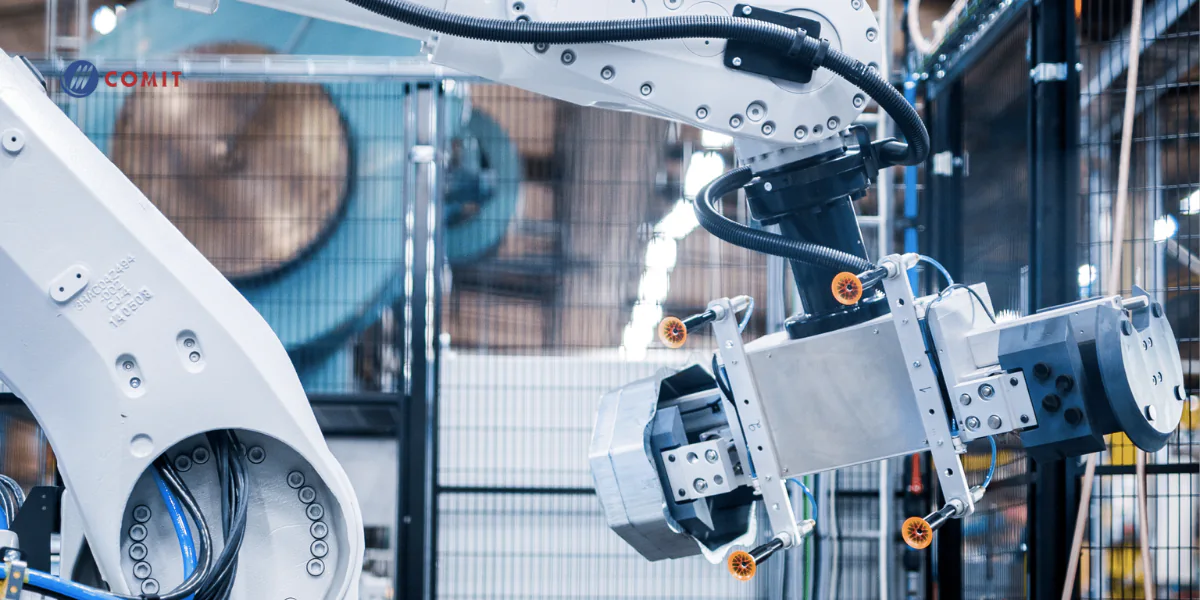
Smart Factory là một hệ thống sản xuất thông minh, tự động hoàn toàn hoặc một phần, được điều khiển và quản lý bằng công nghệ số và Internet of Things (IoT). Các từ đồng nghĩa khác bao gồm sản xuất thông minh, Internet of Things công nghiệp, Industry 4.0, và nhà máy số. Smart Factory nhằm thu thập dữ liệu sản xuất, phân tích nó để đưa ra thông tin chiến lược và sử dụng các thuật toán học máy để nâng cao trí tuệ nhân tạo, tạo ra quy trình sản xuất linh hoạt, hiệu quả và mạch lạc. Điều này giúp tối ưu hóa hoạt động, quy trình và tài sản trong chuỗi sản xuất.
Nên lưu ý rằng một nhà máy thông minh có thể được thay thế bằng các từ đồng nghĩa như: sản xuất thông minh, Internet of Things Industry (thêm thông tin về khái niệm cơ bản của nó), Industry 4.0 và nhà máy số. Tất cả những kết hợp từ ngữ này đều chỉ đến các giải pháp tự động hoàn chỉnh, số hóa và định hình bởi IoT, nhằm thu thập dữ liệu sản xuất, phân tích để đưa ra thông tin hữu ích và tăng cường trí tuệ con người thông qua các thuật toán học máy, nhằm đảm bảo quy trình linh hoạt, hiệu quả và mạch lạc trên mỗi bước của vòng đời sản xuất.
Để đạt được mục tiêu cuối cùng của một cái nhìn toàn diện về quy trình, các hoạt động sản xuất được hỗ trợ bởi IIoT (Internet of Things Industry). Hãy tiến lên và đặt ra các lợi ích và ứng dụng, và làm thế nào thực sự doanh nghiệp của bạn có thể bị ảnh hưởng bởi IoT, cloud computing và phân tích dữ liệu lớn.
IIoT là gì? Tại sao doanh nghiệp trì hoãn việc triển khai nó?
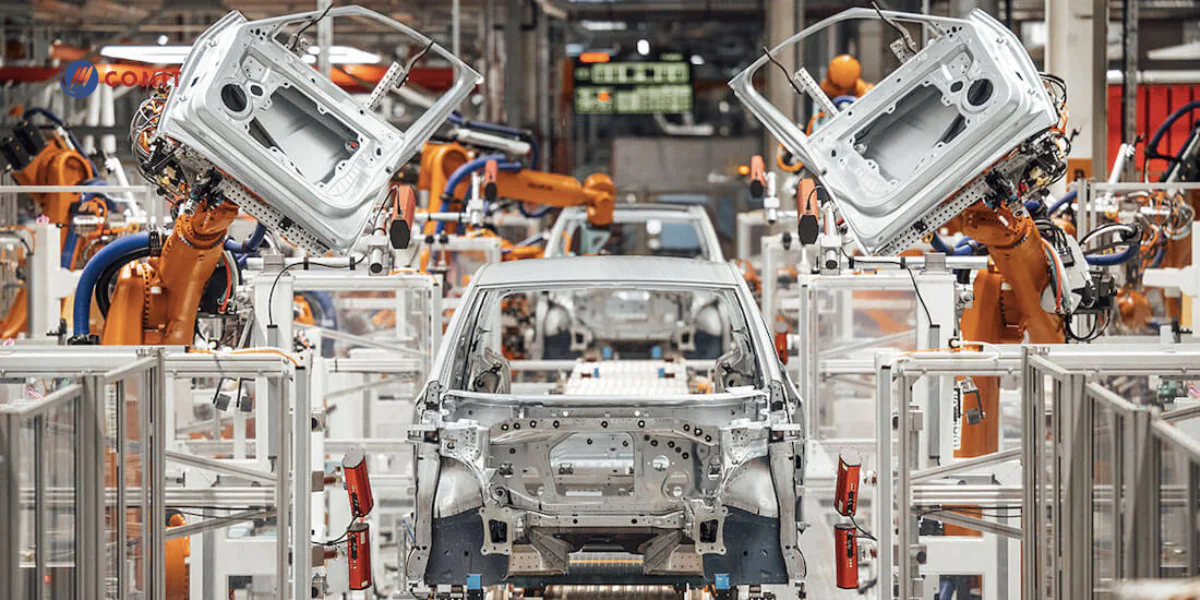
Internet of Things Công nghiệp (IIoT) là cách mà ngành sản xuất có thể tối ưu hóa hiệu suất bằng cách kết nối các tài sản quan trọng, cảm biến, thiết bị, máy móc và robot. Nó nhằm mục đích tối giản hóa hiệu quả vận hành bằng cách thu thập và theo dõi dữ liệu theo thời gian thực để tạo ra thông tin hữu ích. Công nghệ này có thể giúp xác định các tình huống để cải thiện quy trình sản xuất và hỗ trợ quyết định nhanh chóng và chính xác hơn.
Để hiểu rõ hơn về các chi tiết cụ thể, hãy xem xét một trường hợp sử dụng. Bằng cách lắp đặt các cảm biến IoT (ví dụ như có khả năng kiểm tra độ ẩm hoặc nhiệt độ) trên các sản phẩm được vận chuyển từ một điểm đến điểm khác, nhà sản xuất có thể có cái nhìn toàn diện về tình trạng của sản phẩm. Bằng cách theo dõi và giám sát từ xa điều kiện và hiệu suất của tài sản, quản lý có thể đảm bảo rằng điều kiện lưu trữ đúng được cung cấp và nguy cơ hỏng hại được ngăn chặn.
Tuy nhiên, mặc dù nhận ra tiềm năng của nhà máy thông minh để củng cố hoạt động, nhà sản xuất vẫn do dự trước khi tham gia vào hành trình này mà không ước tính giá trị mà họ có thể đạt được và cách hoạt động hiện tại của họ có thể được mở rộng và tăng tốc bằng IIoT. Điều này thực sự là một trong những sai lầm phổ biến nhất của các tổ chức không biết cách đặt ưu tiên đúng. Điều này dẫn đến các đầu tư mạnh mẽ và lãng phí thời gian. Do đó, quan trọng để đánh giá những khả năng mà công nghệ IoT có thể tạo ra, xem xét yêu cầu của khách hàng và mô hình kinh doanh hiện tại trong tổ chức của bạn.
Theo nghiên cứu của McKinsey & Company, có sáu điều mà các doanh nghiệp tin vào, làm hạn chế họ khỏi việc chấp nhận Internet of Things Công nghiệp. Chúng tôi đã phân tích chúng và đặc biệt các điều mà họ tin vào và các rào cản của việc triển khai IIoT và đề xuất các giải pháp để vượt qua chúng:
IIoT sẽ loại bỏ nhu cầu của con người
Người luôn được yêu cầu, đặc biệt là trong quá trình số hóa các quy trình kinh doanh. Điều quan trọng là, cùng với việc thay thế công việc tập trung vào các nhiệm vụ lặp đi lặp lại và nhàm chán, nhà máy thông minh mang lại các công việc mới yêu cầu học các kỹ năng mới. Điều này, lẽ dĩ nhiên, đòi hỏi việc đào tạo lại nhân sự để tận dụng tối đa các công nghệ tiên tiến. Nhưng với những bước tiến lớn, không có cách nào quay lại để không nâng cao khả năng của lực lượng lao động của bạn.
IIoT yêu cầu sự sẵn sàng toàn diện
Kế hoạch lên lịch kéo dài có thể trở thành hoàn toàn không hiệu quả. Theo phương pháp Agile, doanh nghiệp nhanh chóng học từ những thất bại vì phương pháp này cho phép họ thúc đẩy phát triển nhanh chóng và liên tục cải tiến thông qua các chu kỳ phát triển nhanh trong một đến hai tuần.
Nâng cấp không phải là có lợi về chi phí
Ngược lại, thị trường IoT đang phồn thịnh nhờ vào sự giảm giá của cảm biến kết nối. Dựa trên kinh nghiệm của nhiều doanh nghiệp, việc áp dụng các công nghệ thông minh dẫn đến việc hoàn trả chi phí. Và ở đây, chúng tôi phá bỏ một điều kiện về tính không thực hiện được của IIoT đối với thiết bị cũ: bạn có thể tối ưu hóa cơ sở hạ tầng hiện tại của mình với sự thay thế tối thiểu của thiết bị hoặc thậm chí không cần phải thay thế nó. Trụ cột chính để chuyển sang công nghệ nhà máy thông minh là việc mở rộng hệ thống hiện tại bằng cách sử dụng cảm biến, thiết bị và ứng dụng được động lực bởi IoT có khả năng quản lý và kiểm soát đa số công việc. Hơn nữa, bảo dưỡng dựa trên dự đoán có thể loại bỏ đáng kể thời gian gián đoạn và giảm chi phí bảo dưỡng lên đến 40 phần trăm.
Tận dụng Công nghệ Sản xuất Thông minh để Duy trì Sự Dẫn Đầu
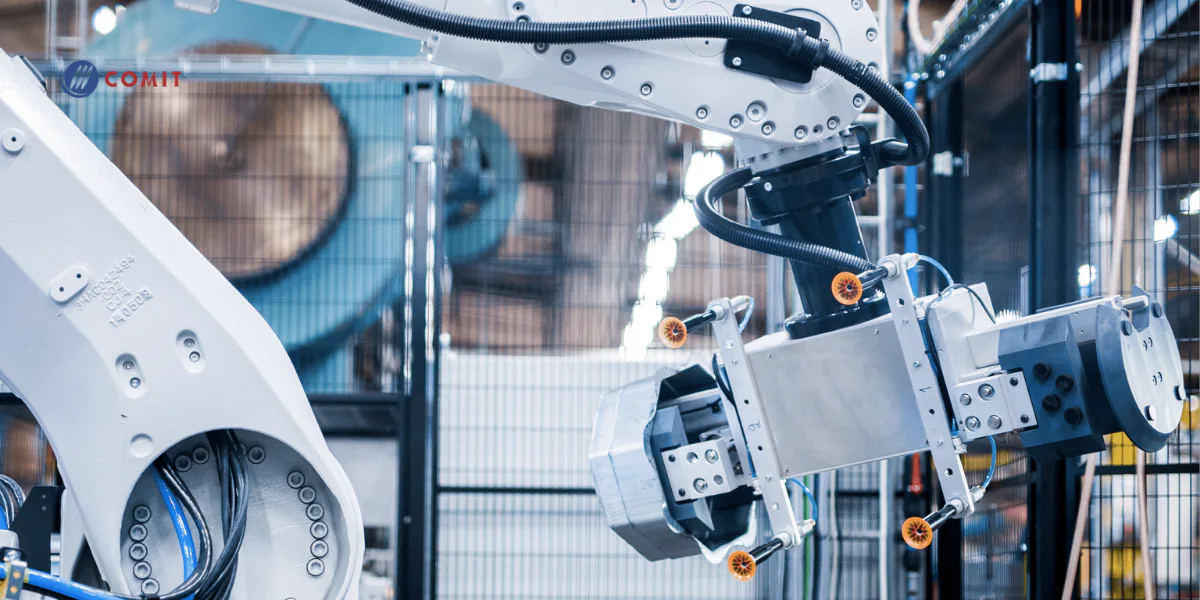
Giám sát theo thời gian thực và quản lý tài sản
Để giám sát những tài sản quý giá nhất theo thời gian thực và quản lý quy trình sản xuất một cách hiệu quả, các doanh nghiệp công nghiệp có thể kết nối chúng và có cái nhìn toàn diện về tất cả các giai đoạn trong suốt vòng đời sản xuất. Tất cả điều này có thể được thực hiện bằng cách triển khai hệ thống theo dõi tài sản và các thiết bị và cảm biến thông minh được lắp đặt vào tài sản trong quy trình sản xuất, chuỗi cung ứng và logistics. Khi được kết nối với nhau, các nhà sản xuất và quản lý sẽ nhận được dữ liệu ở mức độ chi tiết. Dữ liệu này sau đó sẽ được chuyển đổi thành thông tin có ý nghĩa trong hệ thống tập trung nơi các bộ dữ liệu không bị cô lập. Do đó, toàn bộ chu kỳ sản xuất được kiểm soát và tối ưu hóa hoàn toàn nhờ vào báo cáo tự động, cảnh báo thời gian thực và giám sát bảo dưỡng nâng cao.
Với các máy móc được trang bị cảm biến, nhà máy có khả năng tăng cường khả năng nhìn thấy của tài sản vật lý trong môi trường làm việc. Các cảm biến thu thập dữ liệu theo dõi tài sản một cách toàn diện và chính xác. Điều này ảnh hưởng đến việc nâng cao kiểm soát, quyết định chiến lược kinh doanh và báo cáo hàng tồn kho.
Ví dụ: Các giải pháp IIoT của AWS cho phép doanh nghiệp tối ưu hóa chất lượng sản phẩm, tối đa hóa sử dụng tài sản và phát hiện sự cố tiềm ẩn từ trước. Tất cả những ứng dụng này có thể được đạt được thông qua sự kết hợp của công nghệ điện toán đám mây, phân tích dữ liệu tiên tiến và IoT.
IIoT là gì? IIoT là viết tắt của “Industrial Internet of Things,” hay còn được gọi là “Internet of Things Công nghiệp” trong tiếng Việt. Đây là một khái niệm trong lĩnh vực công nghiệp, mô tả sự kết nối của các thiết bị và hệ thống trong môi trường sản xuất sử dụng các công nghệ IoT. IIoT giúp tạo ra một hệ thống thông tin kết nối, cho phép thu thập, chia sẻ, và phân tích dữ liệu từ các thiết bị và máy móc công nghiệp để tối ưu hóa hiệu suất, dự đoán sự cố, và cải thiện quy trình sản xuất. Điều này mang lại nhiều lợi ích, bao gồm tăng cường hiệu quả, giảm chi phí bảo trì, và tạo ra môi trường sản xuất linh hoạt và thông minh hơn.
Quy trình kinh doanh được Tối ưu hóa
Trong khi dữ liệu được theo dõi theo thời gian thực, việc sử dụng tài sản được tối ưu hóa và duy trì tự động, tạo điều kiện cho việc kiểm soát liên tục và điều chỉnh tự động của thiết bị. Điều này không chỉ giúp nhà sản xuất tối ưu hóa chức năng của họ mà còn mở ra cơ hội để điều chỉnh tự động các quy trình.
Hệ thống dữ liệu IoT đã giúp giảm thiểu lượng hoạt động tồn kho bằng cách theo dõi từ xa các tài sản quan trọng. Việc này giảm thiểu sự tham gia thủ công của nhân viên, giải phóng năng lực của họ để tập trung vào quyết định kinh doanh chiến lược. Sự tích hợp của IoT không chỉ mang lại hiệu suất cao mà còn giảm bớt gánh nặng công việc cho người lao động.
Quy trình kinh doanh được tối ưu hóa không chỉ giúp giảm thiểu lỗi, linh kiện thay thế, thời gian chết, mà còn tăng cường kiểm soát chất lượng và nâng cao năng suất của nhân viên. Các quy trình tự động hóa còn mang lại sự linh hoạt, giảm thiểu rủi ro và tăng khả năng thích nghi với biến động của thị trường.
Ví dụ cụ thể, các giải pháp IIoT của AWS đã chứng minh khả năng tối ưu hóa chất lượng sản phẩm, tối đa hóa sử dụng tài sản và phát hiện sự cố tiềm ẩn từ trước. Qua việc tích hợp công nghệ đám mây, phân tích dữ liệu tiên tiến và IoT, các doanh nghiệp có thể thấy rõ sự gia tăng hiệu suất và tăng cường lợi nhuận.
Tổng quan, để đạt được quy trình kinh doanh được tối ưu hóa, doanh nghiệp cần đánh giá kỹ lưỡng tình trạng hiện tại của hệ thống kế thừa, xác định rõ những điểm dữ liệu cần thu thập và phân tích, và áp dụng những giải pháp IoT linh hoạt và hiệu quả. Chỉ thông qua sự tích hợp này, họ mới có thể thấy được toàn bộ tiềm năng của quy trình kinh doanh hiện đại, mở ra cánh cửa cho sự tăng trưởng bền vững và đạt được sự dẫn đầu trong ngành.
Ngăn chặn thời gian chết máy của tài sản thông qua bảo dưỡng dựa trên dự đoán
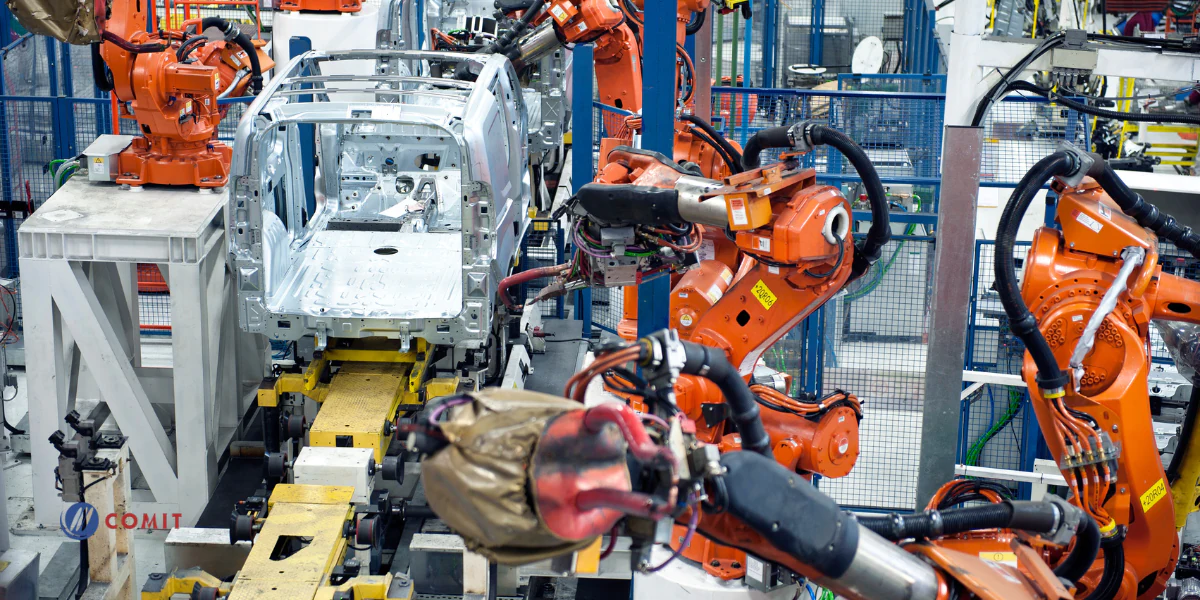
Theo Deloitte, chiến lược bảo dưỡng kém ảnh hưởng đến thời gian chết máy không kế hoạch, từ đó làm suy giảm năng suất sản xuất, trải nghiệm người dùng và doanh thu. Điều này tốn kém cho doanh nghiệp 50 tỷ đô la hàng năm. Có một thách thức liên quan đến việc tối đa hóa khả dụng của tài sản. Doanh nghiệp thường phải đối mặt với vấn đề thương lượng: liệu nên chạy máy cho đến khi hỏng hóc hay thay thế những bộ phận có thể tốt trước. Sử dụng dữ liệu từ nhiều điểm tiếp xúc (cảm biến, ERP, CRM và các hệ thống quản lý bảo dưỡng khác) kết hợp với máy học, bảo dưỡng dự đoán (PdM) đại diện cho một tiềm năng lớn đối với nhà máy. Chúng có thể dự đoán chính xác sự cố và ngăn chặn chúng trước khi xảy ra.
Bảo dưỡng ngăn chặn truyền thống, so với bảo dưỡng dự đoán, bao gồm số lượng người tiêu tốn giờ đồng hồ để thu thập và phân tích thủ công các phần trang thiết bị, kết quả của đó có thể trở nên không chính xác. Bảo dưỡng dự đoán xuất hiện để chiến đấu với thời gian chết máy không kế hoạch bằng cách cung cấp thông tin thời gian thực về hoạt động của thiết bị và đảm bảo rằng tất cả các tài sản được sử dụng một cách hiệu quả nhất và hiệu quả nhất. Quá trình như thế nào? Dữ liệu thu được từ cảm biến nhiệt độ, rung động, độ ẩm, v.v. được chuyển đổi thành tín hiệu số để sau đó được xử lý và phân tích. Sau đó, với phân tích dữ liệu tiên tiến và các thuật toán bảo dưỡng dự đoán, những tín hiệu này được chuyển đổi thành thông tin hình ảnh trên bảng điều khiển (sử dụng API) trên máy tính hoặc ứng dụng trên điện thoại thông minh. Sau đó, chúng được chuyển đổi trở lại thành hành động vật lý dưới dạng cảnh báo bảo dưỡng.
Ví dụ: Bosch Nexeed, nhà máy kết nối tại Blaichach, tích hợp quy trình sản xuất và logistics bằng cách triển khai phần mềm thông minh cho phép thu thập dữ liệu từ 60.000 cảm biến và cung cấp nó theo thời gian thực cho hệ thống Kunz. Với hệ thống theo dõi hiệu suất, dữ liệu có thể truy cập ngay lập tức giữa tất cả các người điều khiển máy, làm cho quy trình sản xuất được ước tính và cải thiện chính xác. Sau đó, các người điều khiển có thể phát hiện sự cố ở giai đoạn sớm nhất và ngăn chặn deviations một cách tích cực để giảm thiểu thời gian chết máy. Kết quả được chứng minh bằng thống kê: năng suất tăng lên đến 25% và hàng tồn kho giảm đi 30%. Hơn nữa, về mặt bền vững, nhà máy tiêu thụ ít nhất 40% năng lượng nhờ vào hệ thống khí nén.
Tối ưu hóa Quản lý Nhân Sự với Robotics Thông Minh
Trong bối cảnh cuộc cách mạng công nghiệp và sự phổ biến của những công nghệ thông minh, Robotics Thông Minh nổi lên như một yếu tố quyết định quan trọng trong việc tối ưu hóa quản lý lao động trong ngành sản xuất. Được định nghĩa là hệ thống trí tuệ nhân tạo có khả năng thu thập và phân tích dữ liệu từ môi trường, robotics thông minh không chỉ quản lý hiệu quả các công việc lặp đi lặp lại mà còn có khả năng hợp tác với con người để đưa ra quyết định kinh doanh tiên tiến dựa trên kinh nghiệm và mô hình học tập trước đó.
Sự tích hợp của cảm biến Internet of Things (IoT) và thuật toán học máy trong lĩnh vực robotics thông minh mở ra những cơ hội mới trong quản lý chuỗi cung ứng và logistics. Những tiến bộ này không chỉ tạo ra sự liên kết toàn diện giữa các giai đoạn trong vòng đời sản xuất mà còn giúp chuyển đổi dữ liệu từ mức chi tiết thành những thông tin có ý nghĩa. Hệ thống tập trung này loại bỏ hiệu ứng siloed, giúp kiểm soát và tối ưu hóa toàn bộ chu kỳ sản xuất thông qua báo cáo tự động, cảnh báo thời gian thực và giám sát bảo dưỡng nâng cao.
Một trong những ứng dụng tiêu biểu của công nghệ nhà máy thông minh sử dụng robotics thông minh là xe tự động hướng dẫn (AGV). Những chiếc xe này có khả năng đảm nhận nhiệm vụ nâng vật nặng và tăng cường quy trình logistics trên sàn nhà máy, tích cực ảnh hưởng đến năng suất và an toàn của nhân viên.
Một ví dụ minh họa điển hình là TRUMPF Group, một công ty sản xuất máy công nghiệp, đã triển khai xe nâng AGV để tự động hóa quy trình di chuyển vật liệu. Giải pháp này không chỉ tăng cường nỗ lực lao động bằng cách tiết kiệm thời gian cho các nhân công chuyên nghiệp mà còn tập trung họ vào các quy trình kinh doanh quan trọng hơn. Điều này là một bước tiến quan trọng trong việc phá vỡ những điều kiện không chắc chắn về việc thay thế con người trong các môi trường sản xuất, đặc biệt là khi tham khảo các ví dụ về AGV trong phần về những lầm tưởng về triển khai nhà máy thông minh.
Digital Twins
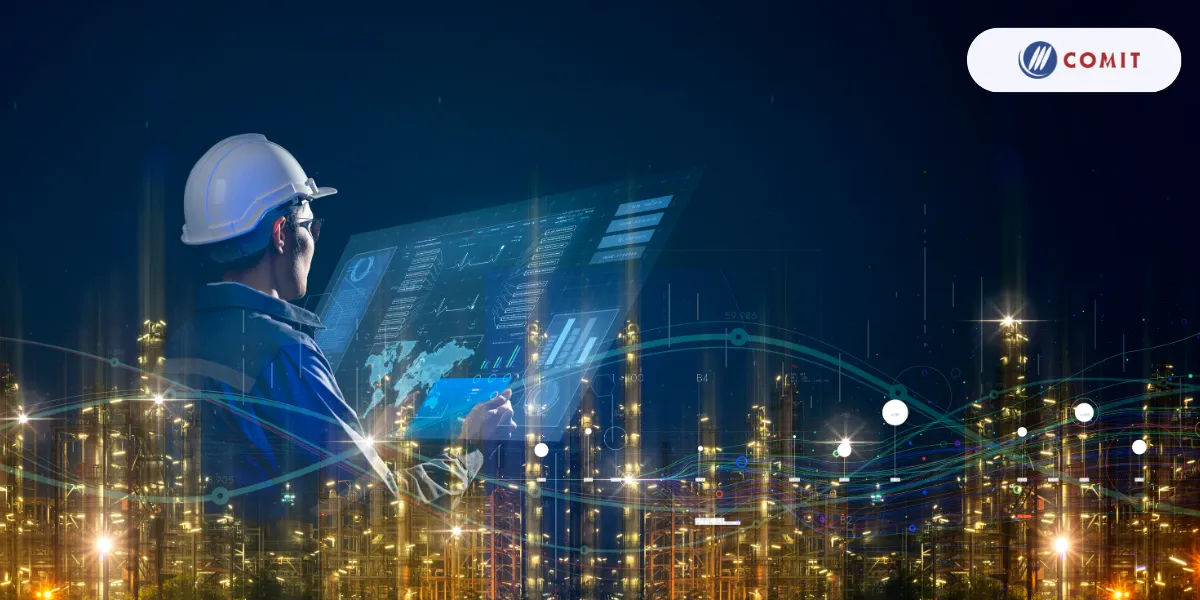
Hãy bắt đầu hành trình khám phá với khái niệm “Digital Twins” – những phiên bản kỹ thuật số tinh tế của mọi đối tượng vật lý trong thế giới thực: quy trình kinh doanh, địa điểm, con người, thậm chí là các thành phố. Đây không chỉ là bản sao đơn giản, mà là sự kết hợp tinh tế của công nghệ IoT, dữ liệu thời gian thực, mô phỏng và học máy, tạo ra những biểu đồ ảo mạnh mẽ dự đoán chính xác và sáng tạo về tương lai của một môi trường kết nối nào đó.
Một “Digital Twin” không chỉ là khái niệm trừu tượng, mà là sự hòa quyện của nó vào thế giới thực thông qua việc áp dụng vào các lĩnh vực như động cơ máy hay động cơ gió. Với trang bị cảm biến IoT, phân tích phần mềm và trí tuệ nhân tạo, “Digital Twin” tạo ra một bản sao kỹ thuật số vô cùng chân thực. Từ dữ liệu thực tế, nó xây dựng các mô phỏng chính xác trong bản sao kỹ thuật số, sau đó áp dụng vào đối tượng vật lý gốc để dự đoán cách chúng sẽ thực hiện.
Ví dụ minh họa cho sức mạnh của “Digital Twins” có thể thấy trong ngành công nghiệp. Đối với việc thu thập dữ liệu kỹ thuật quan trọng về động cơ ô tô, từ sử dụng năng lượng đến nhiệt độ và điều kiện không khí, cảm biến IoT đảm nhận vai trò quan trọng. Nhờ vào “Digital Twins”, ta có cái nhìn chi tiết về hiệu suất, từ đó có thể thực hiện điều chỉnh sản phẩm hoặc các biện pháp khác để đảm bảo hiệu suất sản xuất tối đa.
Ví dụ thực tế từ Nhà máy Siemens Elektronikwerk chứng minh sức mạnh của “Digital Twins”. Sự kết hợp của trí tuệ nhân tạo, máy tính công nghiệp, công nghệ đám mây, robot hợp tác nhẹ và in 3D đã làm tăng sản lượng lên gấp 13 lần kể từ năm 1991. Nhờ vào “Digital Twins”, đội ngũ của Siemens đã giảm thời gian sản xuất các thành phần điều khiển Simatic từ 11 giây xuống còn 8 giây mỗi chu kỳ. Điều này không chỉ là một bước tiến trong công nghệ sản xuất mà còn là cách để xác định nguồn gốc sự cố và ngăn chặn thời gian chết. Hệ thống giám sát thời gian thực giúp cung cấp dữ liệu vận hành cho “Digital Twins” để ngăn chặn thời gian chết và tối đa hóa sử dụng năng lượng hiệu quả thông qua việc áp dụng bảo trì dự đoán.