Quá trình xác định nguyên nhân gốc rễ thất bại của sản phẩm linh kiện điện tử
Những sản phẩm linh kiện điện tử, ngày càng trở nên không thể thiếu trong cuộc sống hàng ngày, đặt ra những thách thức đặc biệt đối với các nhà sản xuất khi phải đảm bảo chất lượng và hiệu suất. Trong quá trình sản xuất, việc xác định nguyên nhân gốc rễ thất bại của các linh kiện trở thành một yếu tố quyết định để nâng cao độ tin cậy và giảm rủi ro. Trong bài viết này, hãy cùng COMIT tìm hiểu về “Quá trình xác định nguyên nhân gốc rễ thất bại của sản phẩm linh kiện điện tử” nhé!
Thu thập dữ liệu
Mục tiêu của quá trình thu thập dữ liệu là để đánh giá và hiểu rõ các sự kiện cũng như các yếu tố nguyên nhân chính liên quan đến sự cố.
Chứng cứ thu thập được sẽ được sử dụng để xác định các khía cạnh quan trọng của lỗi, bao gồm phương pháp, vị trí và cơ chế lỗi, thời điểm xảy ra lỗi trong quá trình vận hành, khoảng thời gian cần thiết để phát hiện và bắt đầu xử lý lỗi, cũng như chu kỳ lỗi.
Các yếu tố “5-P” của việc thu thập dữ liệu bao gồm:
- Mọi người: Tất cả các cá nhân liên quan đến sự kiện và lỗi.
- Bằng chứng vật chất: Tài liệu, dữ liệu, và các thông tin vật chất khác.
- Vị trí (vật lý, trình tự sự kiện thời gian, mối quan hệ chức năng): Nơi xảy ra sự cố, chuỗi sự kiện, và các mối quan hệ chức năng.
- Giấy (thủ tục, sổ tay, nhật ký, e-mail, bản ghi nhớ): Các tài liệu và ghi chú liên quan đến sự kiện.
- Mô hình (quan điểm về các tình huống và phản ứng của chúng ta đối với chúng): Cách chúng ta hiểu và phản ứng với sự cố.
Quá trình thu thập dữ liệu nên được thực hiện ngay sau khi sự cố xảy ra để tránh mất mát hoặc biến đổi dữ liệu có thể ảnh hưởng đến việc xác định nguyên nhân gốc rễ.
Mục tiêu không phải là thu thập một lượng thông tin lớn, mà là tập trung vào dữ liệu có liên quan và quan trọng, tránh thông tin không liên quan gây hiểu lầm.
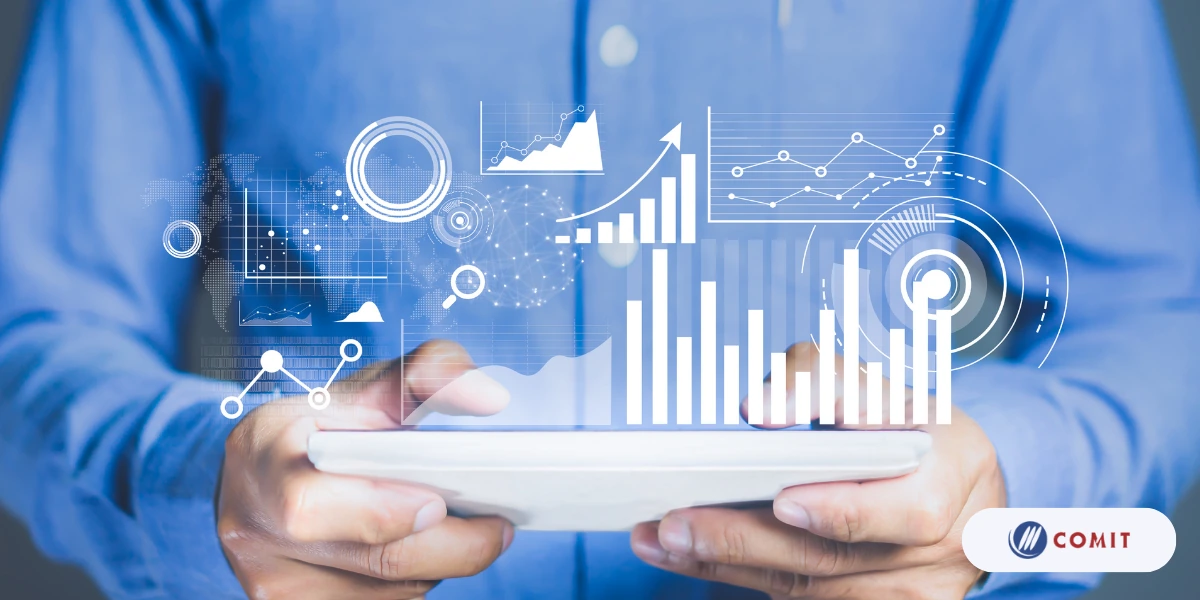
Quy trình đưa ra giả thuyết nguyên nhân bao gồm sử dụng các công cụ như Phân tích ảnh hưởng và phương thức sai lỗi (FMEA), Phân tích mức độ nghiêm trọng và phương thức sai lỗi (FMECA), Phân tích cây lỗi (FTA), Sơ đồ nhân quả – Sơ đồ Ishikawa (phân tích xương cá), Phân tích Pareto và giả thuyết về nguyên nhân.
Phân tích FMEA và FMECA giúp xác định lỗi tiềm ẩn, ảnh hưởng của chúng, cơ chế hư hỏng và cách tránh hoặc giảm thiểu ảnh hưởng của chúng. Phân tích cây lỗi đưa ra cái nhìn từ trên xuống để xác định nguyên nhân cấp cao nhất của sự cố.
Mục tiêu là phát triển cấu trúc và mối quan hệ logic để biểu diễn các sự kiện dẫn đến sự cố, giúp hiểu rõ hơn về xác suất và mối quan hệ giữa chúng.
Phân tích dữ liệu
Bước 2 trong quá trình phân tích dữ liệu sau khi thu thập là xem xét cẩn thận các thủ tục nội bộ, bao gồm thiết kế, quy trình sản xuất, mua sắm, lưu trữ, xử lý, kiểm soát chất lượng, bảo trì, chính sách môi trường, an toàn, quy trình liên lạc hoặc đào tạo. Việc so sánh các thủ tục nội bộ này với các tiêu chuẩn, quy định tương ứng hoặc tài liệu của nhà cung cấp bộ phận và thiết bị là một phần quan trọng để xác định nguyên nhân gốc rễ của sự cố và lên kế hoạch hành động khắc phục.
Ví dụ, việc sử dụng sai một thành phần có thể phát sinh từ việc sử dụng nó ngoài các điều kiện vận hành do nhà cung cấp chỉ định, như dòng điện, điện áp hoặc nhiệt độ. Điều này có thể dẫn đến việc hiểu lầm về yêu cầu vận hành cụ thể và tăng khả năng xảy ra lỗi.
Một ví dụ khác có thể liên quan đến việc sử dụng sai thiết bị, chẳng hạn như thiết bị lắp ráp, làm lại hoặc kiểm tra. Nguyên nhân có thể xuất phát từ sự thay đổi không kiểm soát được yêu cầu vận hành của máy, có thể là do sửa đổi không được ghi lại hoặc không được kiểm soát đúng cách.
Ngoài ra, một lỗi có thể xảy ra do hiểu sai hướng dẫn lắp ráp được viết kém. Nếu nhân viên không hiểu đúng cách thực hiện các bước lắp ráp hoặc có thông tin không chính xác từ tài liệu hướng dẫn, điều này có thể dẫn đến lỗi trong sản xuất hoặc vận hành.
Bằng cách xác định các khác biệt giữa thực tế và các tiêu chuẩn hoặc quy định, người phân tích có thể đặt ra các giả định và đề xuất các hành động cụ thể để khắc phục những nguyên nhân gốc rễ và nâng cao quy trình.
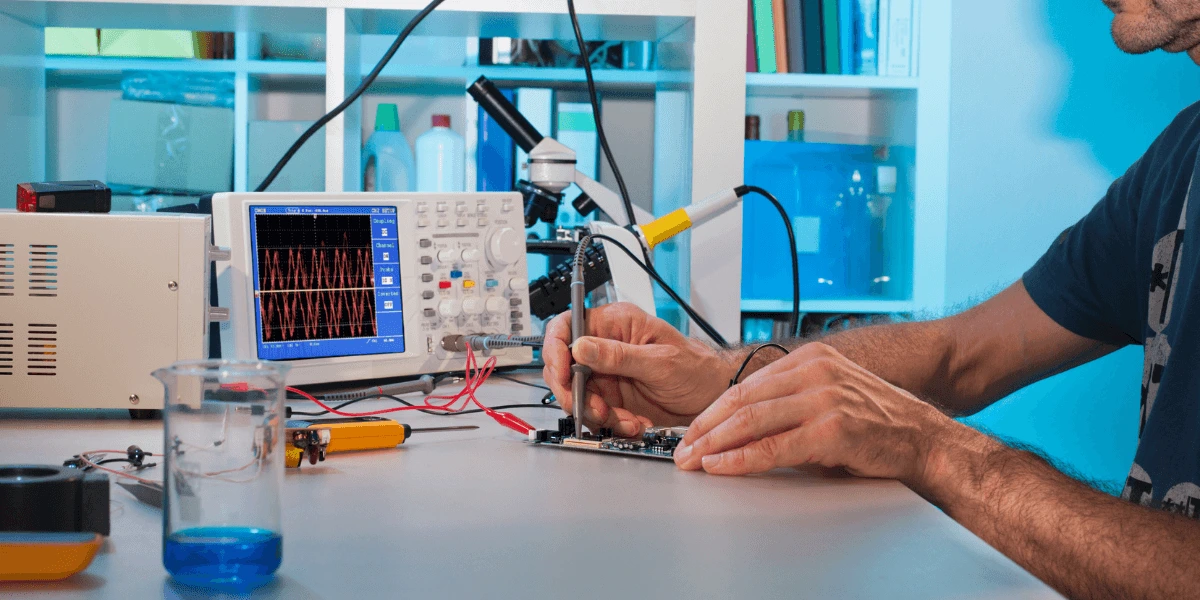
Kiểm tra phân tích lỗi
Phân tích nguyên nhân gốc rễ của lỗi sử dụng nhiều thử nghiệm khác nhau để xác định nguồn gốc thực sự của lỗi sản phẩm linh kiện điện tử. Các thử nghiệm này được chia thành hai loại: thử nghiệm không phá hủy, giúp giữ nguyên sản phẩm; và các thử nghiệm phá hủy, đòi hỏi sản phẩm phải được thay đổi để kiểm tra mặt cắt ngang hoặc đặc tính nhiệt.
- Kiểm tra không phá hủy (NDT):
- Kiểm tra trực quan
- Kính hiển vi quang học
- Chụp ảnh tia X
- Quang phổ huỳnh quang tia X
- kính hiển vi âm thanh
- Phân tích khí dư
- Kiểm tra độ kín
- Kiểm tra phá hủy:
- Phân tích nhiệt
- Phân tích vật lý phá hủy (DPA)
- Phân tích mặt cắt ngang
Kiểm tra không phá hủy (NDT) là gì? Kiểm tra không phá hủy (Non-Destructive Testing – NDT) là một phương pháp kiểm tra và đánh giá chất lượng của vật liệu, sản phẩm hoặc cấu trúc mà không làm hỏng hoặc làm thay đổi tính chất của chúng. NDT được sử dụng để phát hiện các khuyết tật, lỗ hổng, hay bất kỳ vấn đề nào ẩn sau bề mặt của vật liệu mà không cần phải phá hủy mẫu.
Việc liên tục đưa các sản phẩm chất lượng cao và đáng tin cậy ra thị trường đòi hỏi một quy trình kỹ thuật được tối ưu hóa trong thiết kế sản phẩm – quy trình cho phép nhà phát triển nhanh chóng xem qua hàng chục trăm lựa chọn thay thế thiết kế khác nhau mà không cản trở việc giao hàng đúng hạn. Làm thế nào các công ty đạt được điều này? Họ sử dụng giải pháp mô phỏng tự động.
Các công ty hàng đầu đã chuyển sang sử dụng các giải pháp mô phỏng cho phép các công ty di chuyển nhanh chóng trong quá trình thiết kế sản phẩm của mình mà không phải chi quá nhiều chi phí. Lợi ích của mô phỏng vượt xa chi phí ban đầu và thiết lập về lâu dài, vì nó cung cấp một môi trường chi phí thấp, không rủi ro cho phép các nhà thiết kế xem xét hàng trăm, nếu không phải hàng nghìn lần lặp lại của cùng một thiết kế. Mô phỏng như một phần của quá trình phát triển sản phẩm đang được phổ biến rộng rãi. Việc sử dụng mô phỏng như một phương tiện để giải quyết các thách thức về độ phức tạp ngày càng tăng của sản phẩm và cải thiện độ tin cậy là chủ đề quan trọng nhất.
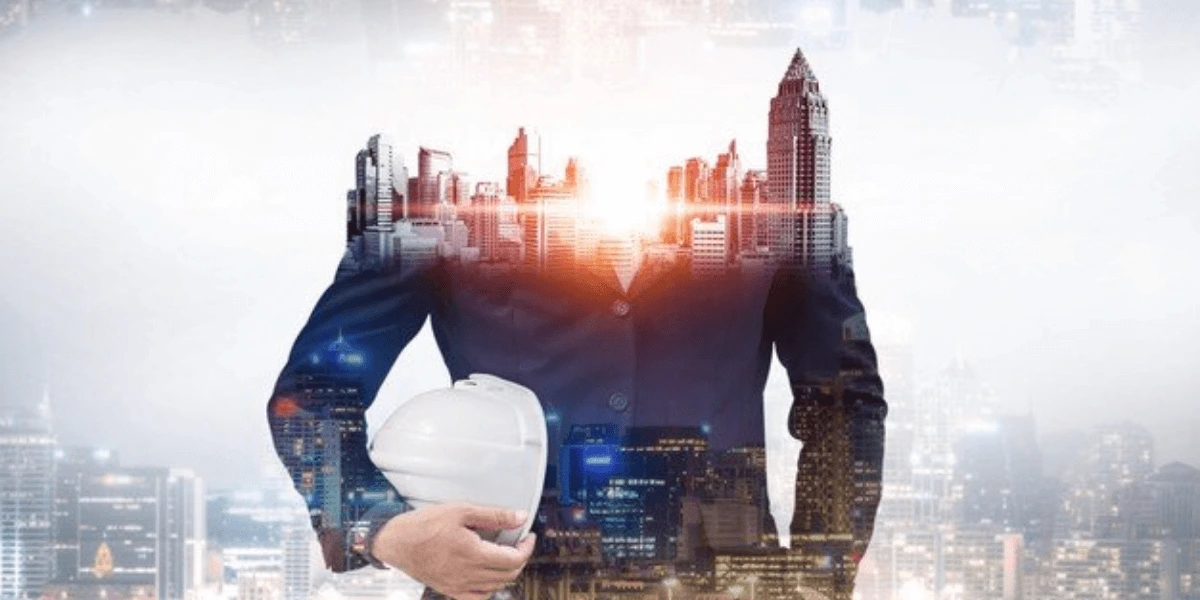
Dưới áp lực liên tục phải tung ra những sản phẩm thực sự sáng tạo một cách nhanh chóng và đáng tin cậy, các công ty cần có khả năng đáp ứng nhu cầu của người tiêu dùng trong khi vẫn duy trì được lợi nhuận. Đối với các công ty hàng đầu, điều này có nghĩa là sử dụng giải pháp gói mô phỏng. Để tận dụng đúng lợi ích của mô phỏng, các công ty nên tìm kiếm các giải pháp cho phép khám phá các phương án thiết kế khác nhau trên các môi trường khác nhau. Để triển khai mô phỏng đúng cách trong quá trình phát triển sản phẩm, hãy làm theo các bước sau:
- Tải trước quá trình phát triển sản phẩm: Thực hiện phân tích và kiểm chứng chặt chẽ nhất trong một số giai đoạn đầu tiên. Những thay đổi ở giai đoạn đầu dễ dàng được điều chỉnh và ít tốn kém hơn so với những thay đổi trong quá trình sản xuất. Việc lặp lại thiết kế càng sớm được khám phá thì khả năng thay đổi càng linh hoạt hơn và càng có ít chỗ cho lỗi ở khâu sau. Cách dễ nhất để thực hiện việc khám phá này là sử dụng mô phỏng và tạo mẫu ảo.
- Điều chỉnh công nghệ để phù hợp với con người và quy trình của bạn: Thêm các giải pháp dễ sử dụng và sẽ dễ dàng tích hợp vào quy trình của bạn. Hãy nhớ rằng bất kỳ giải pháp mới nào cũng cần được đào tạo, đây cần được coi là một phần quan trọng của quá trình tích hợp. Sử dụng các giải pháp mô phỏng sẽ hỗ trợ giảm lỗi trong quá trình thiết kế và chức năng, đồng thời phù hợp với quy trình hiện có.
- Sử dụng các giải pháp giúp tiêu chuẩn hóa thiết kế và lưu trữ hồ sơ của tổ chức về “bài học kinh nghiệm” và gỡ lỗi tiếp theo: Các công ty tốt nhất có xu hướng sử dụng mô phỏng trong phân tích lỗi sau sản xuất cao hơn 33%.
- Giữ sự hợp tác chặt chẽ giữa các nhóm thử nghiệm và thiết kế: Các giải pháp cải thiện hiệu suất sản phẩm chỉ có thể được sử dụng hiệu quả nếu thông tin đó được chuyển đến các nhà thiết kế.
Các công ty có thể giảm đáng kể chi phí sản xuất, giảm sự chậm trễ khi đưa sản phẩm ra thị trường và cải thiện độ tin cậy của sản phẩm linh kiện điện tử bằng cách thực hiện các bước phù hợp để triển khai hiệu quả thử nghiệm và mô phỏng trong quá trình phát triển sản phẩm của mình. Điều này đòi hỏi một cách tiếp cận có hệ thống trên toàn bộ doanh nghiệp, bằng cách triển khai các khả năng giải pháp mô phỏng và thử nghiệm để trang bị cho người dùng làm việc hiệu quả và năng suất.